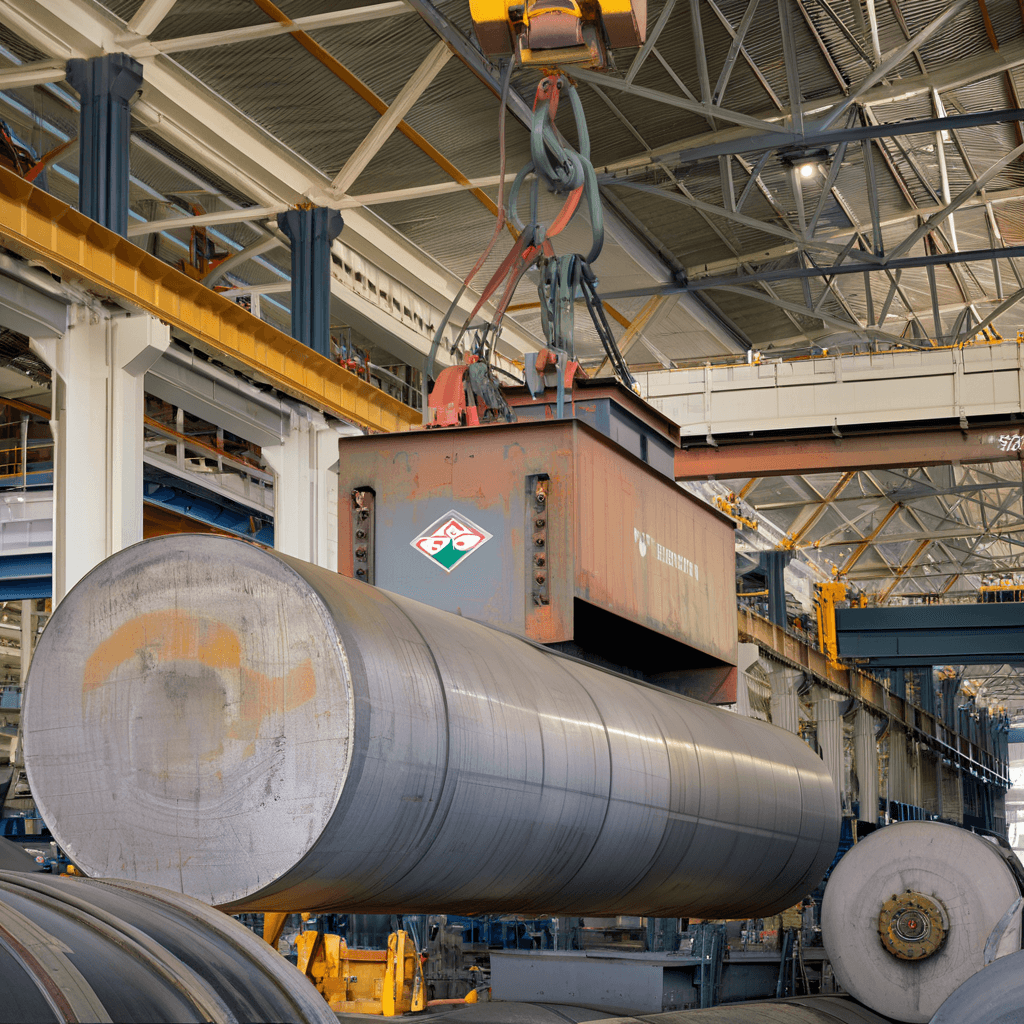
1045 Steel | ASTM 1045 | ASSI 1045 | C45 Round bar | EN8 Round Bar
ASTM 1045 steel is characterized by good weldability & machinability, and high strength and impact properties in either the normalized or hot-rolled condition.
ASTM 1045 steel has a low through-hardening capability with only sections of around 60 mm in size being recommended as suitable for tempering and through-hardening. However, it can be efficiently flame- or induction-hardened in the normalized or hot rolled condition to obtain surface hardnesses in the range of Rc 54 - Rc 60 based on factors such as section size, type of set up, quenching medium used etc.
Designation by Standards
Chemical Composition (%)
Mechanical Properties
Typical Mechanical Properties - Hot Rolled Condition
Typical Mechanical Properties - Normalised Condition
Elongation in 50mm %
Machining
ASTM 1045 steel has good machinability in a normalized or hot-rolled condition. Based on the recommendations given by the machine manufacturers, operations like tapping, milling, broaching, drilling, turning can be carried out on ASTM 1045 steel using suitable feeds, tool type, and speeds.
Welding
ASTM 1045 steel is readily welded when the correct procedure is followed, but welding ASTM 1045 steel in through-hardened, tempered and flame- or induction-hardened conditions is not recommended. Low hydrogen electrodes are preferred for welding ASTM 1045.
Heat Treatment
ASTM 1045 is subjected to forging, annealing, normalizing, stress-relieving, hardening and tempering processes – each of which is explained in more detail below:
- Forging - Heat to 850°C - 1250°C (1562°F - 2282°F).
- Annealing - Heat to 750°C - 820°C (1472°F - 1562°F).
- Normalizing - Heat to 860°C - 900°C (1598°F-1688°F). Hold until the temperature is uniform. Soak for 10 - 15 minutes.
- Stress-Relieving - Heat to 550°C - 660°C (1022°F - 1220°F). Hold until the temperature is uniform. Soak for 1 hour per 25mm of section.
- Hardening - Heat to 820°C - 850°C (1508°F - 1562°F). Hold until the temperature is uniform. Soak for 10 - 15 minutes per 25mm of section.
- Tempering - Re-heat to 400°C - 650°C (752°F - 1202°F) as required. Hold until the temperature is uniform. Soak for 1 hour per 25mm of section.